We use cookies to personalise content & improve our services. By using our site, you consent to our Cookie Policy. Read more
Unique technology hidden in the core of hand-built Finnish de luxe boats – data helps to save yachtsmen in trouble
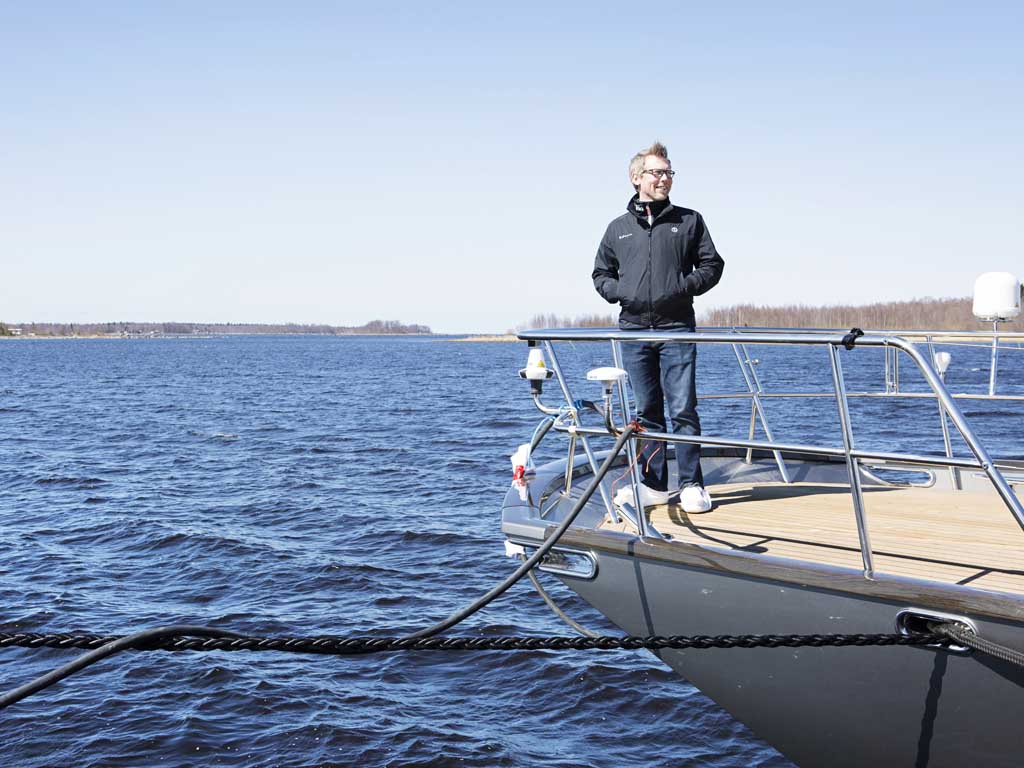
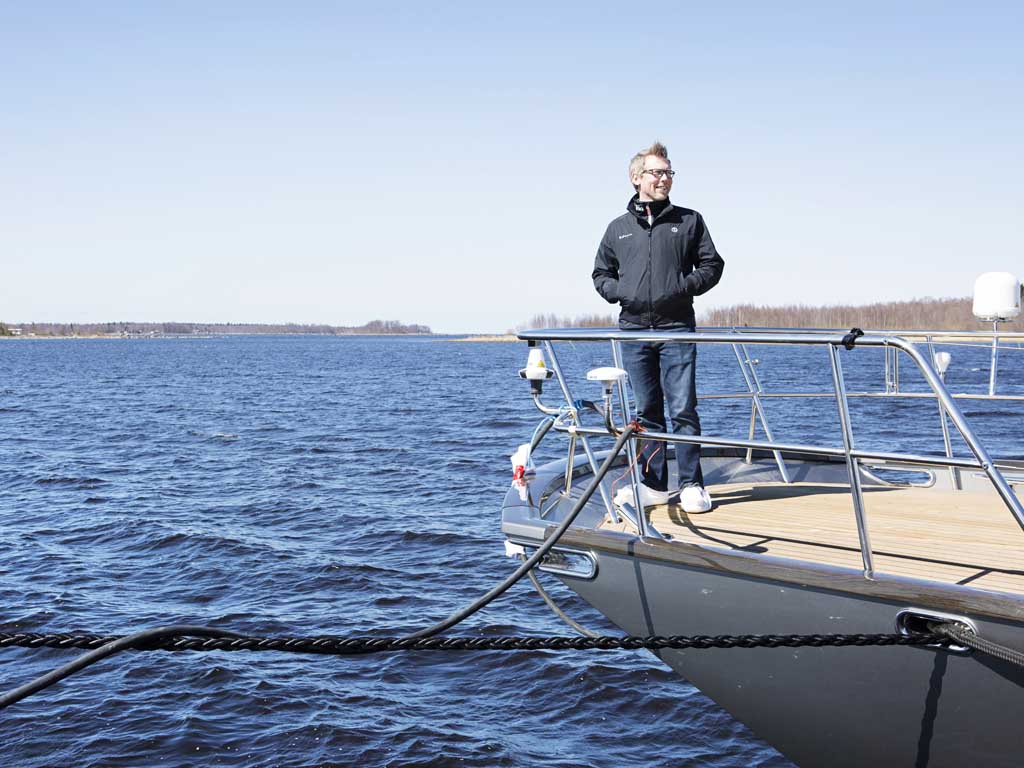
At the heart of de luxe boats built in Ostrobothnia lies a piece of completely unique technology. Combining a craftsmanship tradition spanning hundreds of years with the famous Finnish expertise in technology, Baltic Yachts gets orders from all over the world. The names of the buyers – even the richest and the most famous – are kept absolutely secret.
Sun rays are reflected by the body of an enormous mast like it was made of mirror glass. The mast is lying flat in the site of Baltic Yachts harbour, waiting to be erected. Today, the wind is too strong for the job.
Sasha Laitinen, financial manager at Baltic Yachts, walks by the mast towards a 175-foot carbon fibre sailing boat to be crowned by the gigantic mast on any day now.
“The boat was launched last Friday. A total of 70 people have been working on it, including the future captain and the crew. They need to learn to use the boat’s technology.”
Learning, indeed, is necessary: in addition to the steering system, gauges, entertainment systems and engines, the boat contains some new technology solutions not found anywhere else in the world. (Article continues below)
Unique design
Laitinen puts on shoe covers and strides to the deck of the brand new boat. Wearing shoes while walking around the boat is strictly forbidden to avoid staining the carefully chosen pale blond wooden panels.
“All technology is now hidden under the interiors,” says Laitinen, passing through the living room towards the bedroom wing.
Every boat ordered from Baltic Yachts is unique. Customers’ orders are met up to the tiniest detail. All interior design solutions are kept strictly between the customer, the designer and the builder and not revealed to anyone else.
“What makes us famous is that you can tell us your wildest dreams, and we will make them true,” Laitinen smiles.
A boat steered like a car
“Our strong suit is that we do everything ourselves. We have a reputation of being pioneers in developing technology solutions,” Laitinen says, showing the electronic force feedback steering system developed by Baltic Yachts that makes it possible to freely adjust the helm touch.
The applied technology is, in practice, the same as in modern cars.
“With this system, it is possible to customise the helm touch for different users or needs,” Laitinen explains.
In addition to unique boat technology, the company has developed noise and vibration insulation and increasingly lightweight materials aimed at maximising the speed of boats.
Together with Telia, Baltic Yachts is developing a concept for its Internet of Things solutions and data application. Currently, Baltic Yachts is using Telia’s voice and data solutions.
“Internationally accessible networks and data flows play a significant role in our cooperation with Telia. Our service teams around the world need data to do their work.”
Data saves you from trouble
Data comes to the rescue of an yachtsman in trouble. If the steering system fails, an engine part stops functioning, a boat’s exterior is damaged or something similar happens, Baltic Yachts service team is called to help.
“We will have a team there within two or three days of the alert. The place may be the Caribbean Sea or the Indian Ocean, near a small island or wherever.”
When working, the service team needs to know which materials have been used in the boat and how its technology has been constructed. Networks are necessary to transmit this information. If there is no data, fault diagnosis becomes more difficult. (Article continues below)
“It takes a while to find the right part here if you don’t know where you should be looking,” Laitinen says at the door of an overfull engine room.
Since the crew is responsible for maintenance, the service team is not called to help in small failures. In the future, engine parts, controls and other equipment will be able to signal their repair needs independently.
“I expect that my car lets me know when it’s time to take it to be repaired. I’m sure that in the future, customers are expecting boats to do the same.”
It is envisaged that data will help in optimising system components to correspond better to the special needs of customers, and it will become possible to help the crew remotely.
It is still very windy on the deck when Laitinen leaves the cabin and climbs back to daylight. He heads towards the factory standing by the harbour area.
Handicrafts at an industrial scale
Inside the factory, the air is humid and cool. The sound of drilling is mixed with the booms of a hammer. There is an aroma of wood in the air. The hall building can house two de luxe boats at a time, each of them more than 150 feet long. Humidifiers keep the conditions just right.
“The relative humidity of the air mimics that of the Mediterranean Sea, because that is the kind of climate where the boats will be used. The composite materials used in construction react to variations in air humidity.”
A mould for the body of a new boat towers in front of the back wall. The floor is full of body mould parts that look like huge pieces of a puzzle. They will be attached together with a hammer before fitting. (Article continues below)
“This is handicrafts at an industrial scale. We use our expertise to do what we know best and continue a tradition that spans hundreds of years.”
The sailing boat under construction will stay in the hall until next year. But the yacht floating outside in the harbour will sail away with its crew in July.
“Boats sail off along the main passage, and when they reach the lighthouse, they take a turn towards international waters. After that, we won’t see them again.”
Global operations require global reliability
Challenge: Meeting customers’ wishes requires new technology solutions not found anywhere else in the world. When problems arise, the service team goes the extra mile – or thousand miles, if need be – to fix the unique systems. Problem-solving requires data with which the fault can be found and fixed.
Solution: Telia’s globally operating network ensures data transmission for the needs of the service team anywhere in the world. In co-operation with Telia, Baltic Yachts is developing a concept for the creation of new IoT solutions.