We use cookies to personalise content & improve our services. By using our site, you consent to our Cookie Policy. Read more
The world’s first industrial 5G artificial intelligence application was created in Finland – “This calls for Finnish grit”
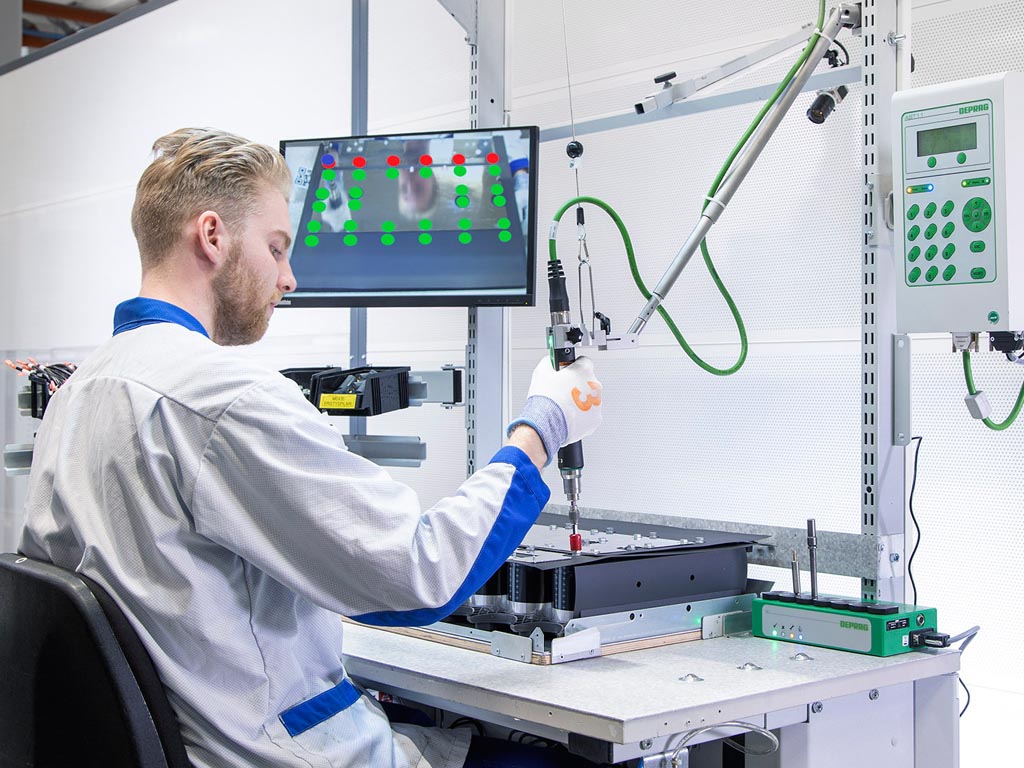
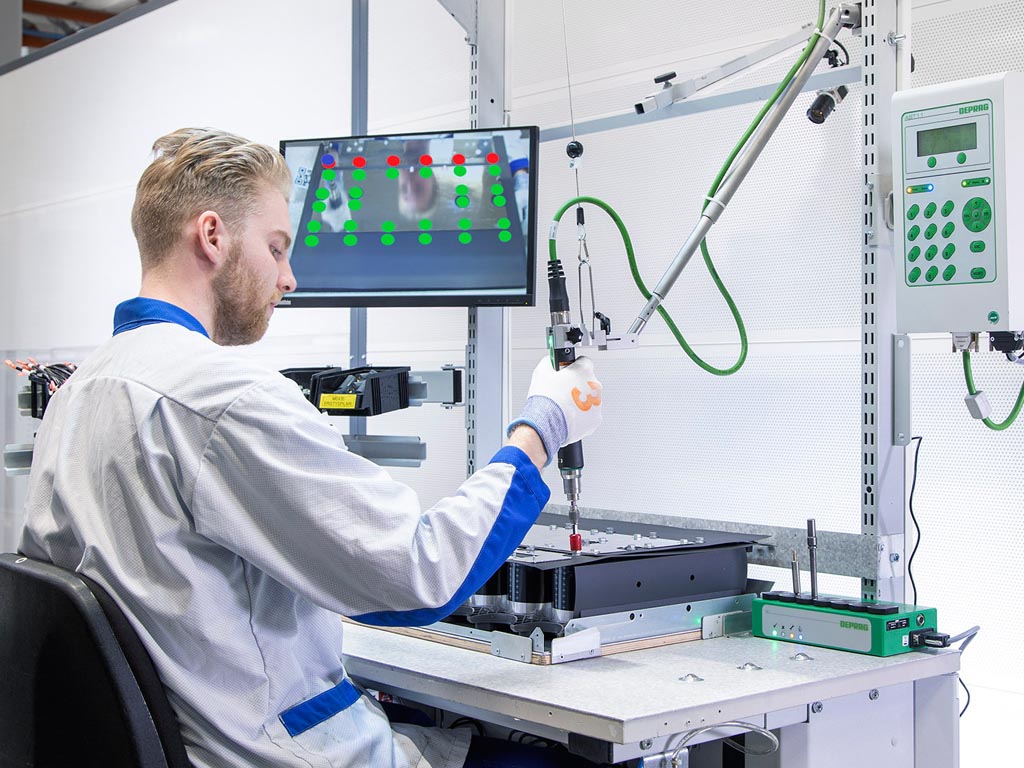
Leevi Pienihäkkinen lifts some capacitors off a shelf and arranges them in the correct places. 5G technology and a machine vision application have come to the workstation, making installation work easier by eliminating the stress of whether the model really was assembled correctly and the worry over whether all of the screws were properly tightened. Pienihäkkinen makes frequency converter modules at ABB’s factory, and any errors could be disastrous. For example, an incorrectly assembled module could stop a cargo ship in the middle of an ocean. The employees have vast amounts of expertise and know-how, but when countless modules are assembled every day, there is always the chance of an error creeping in.
“The screen gives me instant feedback if something has gone wrong in the installation,” explains Pienihäkkinen. “The screen shows the sequence in which the capacitors should be arranged, and the application also checks that they have been installed in the module the right way round.”
The smart solution at Pienihäkkinen’s workstation is the world’s first industrial 5G artificial intelligence application, and it has been deployed at ABB’s frequency converter factory in Helsinki. The solution utilises a real-time video feed, which is delivered to Telia’s data centre over an ultra-fast 5G network for artificial intelligence to analyse. Artificial intelligence cannot interpret a pixellated mess, so a high-quality video feed is needed.
“The volume of data transferred is enormous, so 5G capacity is required. 5G is also ideally suited to this application because the feedback generated by artificial intelligence is required immediately,” says Digital Lead Simo Säynevirta from ABB in Finland.
The solution makes a difference to occupational wellbeing: “The worry and stress of installation errors is eliminated. The best results are realised when smart systems work together with people,” says Säynevirta. “The solution also increases productivity, as in practice, the application will enable 100% quality. In addition to the Helsinki frequency converter factory, it is also important to ensure high quality on a global scale, and the application enables this.”
5G is the key to the fourth industrial revolution
“5G was made for this,” says Janne Koistinen, Telia’s 5G Programme Director, referring to the application launched at ABB’s factory. “It must be possible to alter production lines more flexibly and modify systems as quickly as possible. When cloud services are utilised, the changes can be implemented in every location straight away. The cloud also offers unlimited computing capacity, and 5G enables latency-free wireless connectivity to the cloud.”
The network’s extreme reliability and low latencies are very important in a factory setting. The fifth generation of networks was designed to support the development of applications such as Industry 4.0 environments and smart traffic. Koistinen emphasises that the greatest value in 5G is not the network connection but the fact that data is collected and refined, and that artificial intelligence is used for purposes such as data analysis: “This gives rise to opportunities to create new types of digital business.”
“The key aspect of 5G pilot projects is to identify the applications where 5G can enable productivity to be increased. The leap in productivity enabled by 5G may end up being enormous. According to GSMA’s report, the mobile industry may generate up to USD 850 billion in global economic growth between 2018 and 2023. However, companies will need to work together to make use of new technologies, and legislation will be required to permit steps into the unknown. And, of course, this also requires some good, old-fashioned Finnish grit – that is why the application was made in Finland,” Koistinen laughs.
“Five years ago, it would have taken much longer to develop a solution like this,” says Mika Torhola, Managing Director of Atostek Ltd, the company that developed the machine vision and artificial intelligence application running in ABB’s factory. “Now the application has been in use for a few months. This is the solution that makes Gartner’s hype cycle a reality.”
A solution in practice
The artificial intelligence solution supports the employee by using a video camera to monitor the assembly of frequency converters and ensure that the device is correctly assembled according to the customer order and the product’s work instructions. Fast connections enable installation engineers to receive real-time, latency-free feedback on their work, which is expected to significantly facilitate assembly in comparison with work instructions on paper.
The project was executed in collaboration with Atostek Ltd, a specialist in demanding industrial applications, and Telia. Atostek is responsible for the project’s machine vision and artificial intelligence application, while Telia implemented the ultra-fast 5G mobile connections for the system and is responsible for the computing capacity required by the artificial intelligence application in its data centre.